Environmental Sustainability at Asahi
Our beverages bring enjoyment and connection to everyday moments in life. We are committed to ensuring Australians and New Zealanders can celebrate these moments in a more sustainable way that reduces the impact on our planet.
As Oceania’s leading beverage company, we are using our significant scale to deliver positive change through our operations and partnerships.
Our Environment Management System
Environmental Compliance and Management
Our first and most critical commitment is compliance with our environmental legal obligations. We have implemented an Environmental Management System (EMS) to manage our impacts on the environment and drive continuous improvement in our environmental performance. We have achieved external EMS certification (ISO14001) at seven of our manufacturing sites. Further detail can be provided on request.
Our Environment Policy sets out our company commitments and strategies. Read the document here.
Our Environmental Commitments
- Compliance: Meet our environmental legislation and other relevant obligations
- Accountability: Providing our people with the skills and knowledge to uphold our environmental responsibilities
- Management of systems: Implement and operate an effective environmental management system
- Improving environmental impact: Identify all points where we impact the environment and take action to eliminate, minimise or mitigate their impacts
- Continual improvement: Establish, measure and review objectives and targets to continually reduce our impact on the environment
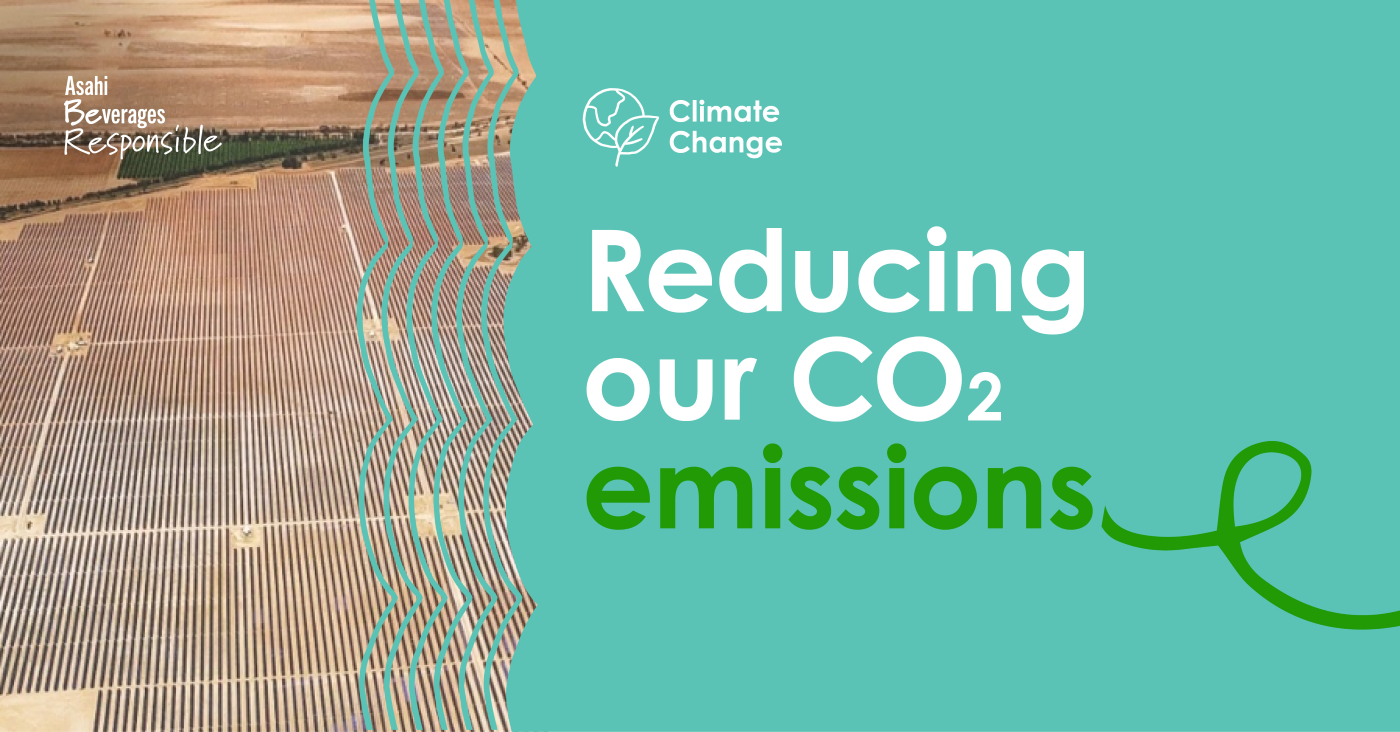
Climate Change
The climate is changing and the consequences will be far-reaching.
Asahi Beverages recognises we can use our large supply chain and extensive partnerships to drive positive climate action.
To help tackle this issue, 100% of our purchased electricity will be sourced from or matched with renewable sources by the end of 2025. This will involve scaling our on-site solar generation to reduce what we purchase, and matching our remaining energy requirements through Power Purchase Agreements which support the development of renewable energy projects.
What we are targeting - our Climate Change goals:
- 100% of our purchased electricity to be sourced from or matched with renewable sources by 2025
- Reduce Scope 1 & 2 CO2 emissions in our operations by 50% by 2025*
- Reduce Scope 3 CO2 emissions by 30% by 2030*
*vs a baseline year of 2019
Some of our initiatives so far:
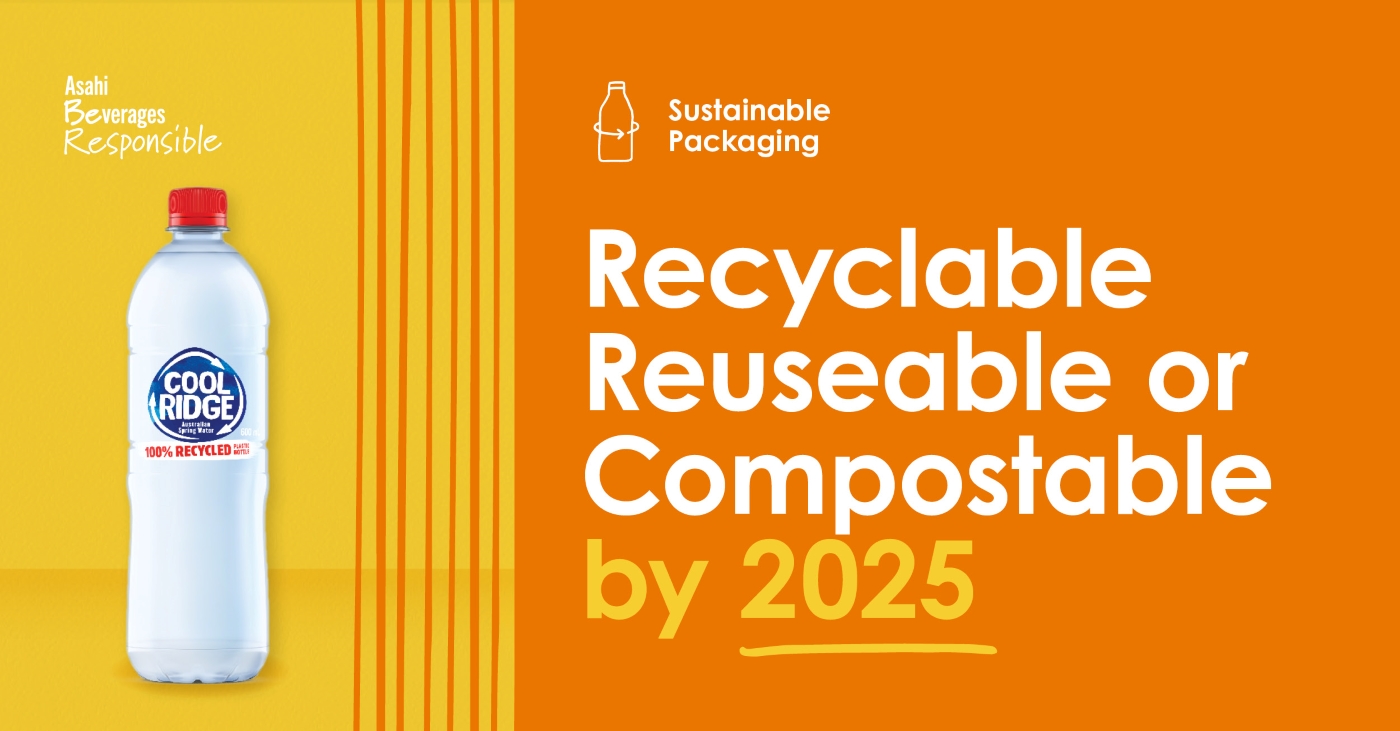
Sustainable Packaging
More waste is entering the environment each year, putting pressure on ecosystems and contributing to greenhouse gas emissions.
Asahi Beverages is tackling this global problem and has committed to designing our bottles and cans to be more sustainable.
100% of our primary packaging will be recyclable, reusable or compostable by the end of 2025. Primary packaging means cans and bottles (excluding cap and label).
Whilst our bottle caps are made from recyclable material and are recyclable, we do understand that different local councils and Container Deposit Schemes may have different approaches to the recycling of caps.
We acknowledge the current suspension of soft plastics recycling in Australia, and recognise that APCO have confirmed that it is unlikely that the 2025 National Packaging Targets will be met. Nevertheless, we remain committed to supporting workable industry initiatives to reintroduce soft plastics recycling as soon as possible.
What we are targeting - our Sustainable Packaging goals:
- 100% of our primary packaging will be recyclable, reusable or compostable by the end of 2025. Primary packaging means cans and bottles (excluding cap and label)
- Increase the amount of recycled content used in our glass bottles and aluminium cans to on avg. majority (50>%) recycled content by 2030
-
Transition to 100% eco-friendly materials for PET bottles (excluding cap and label) by 2030. Eco-friendly means either compostable, bio based or 100% recycled content
Some of our initiatives so far:
- Leading beverage companies to help deliver new Victorian container deposit scheme
- Cool Ridge water bottle (excluding cap and label) now made with 100% recycled PET (rPET)
Our Australian Packaging Covenant Report:
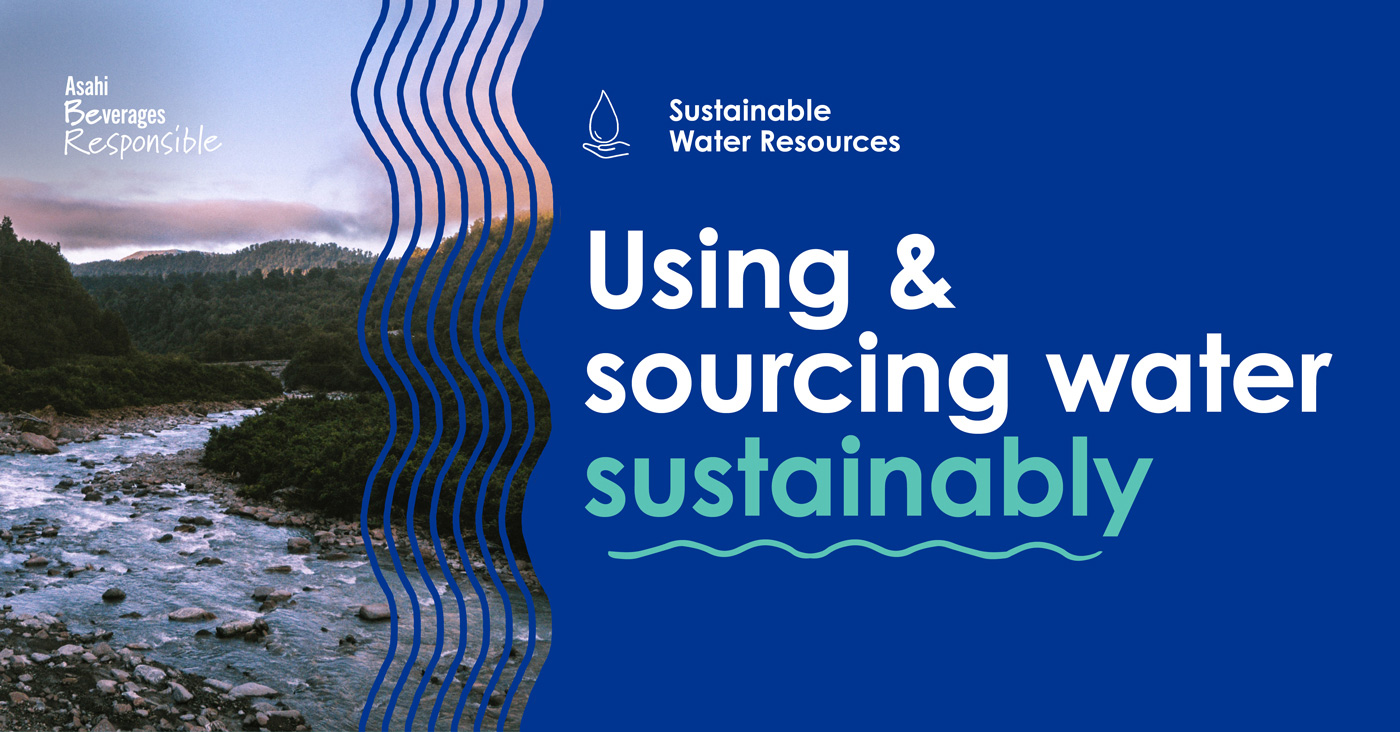
Sustainable Water Resources
Water is an essential ingredient in each of our products, which is why we’re committed to its ongoing sustainability.
We are taking steps to reduce water use at our key manufacturing sites with a goal that by 2030 we'll use just 2.19 litres per litre of beverages we produce.
We regularly conduct water risk assessments at our key manufacturing sites to understand our water usage.
What we are targeting - our Sustainable Water Resources goals:
- Conduct Water Risk Assessments at our key manufacturing sites
- Reduce water use at our key manufacturing sites by 2030 to just 2.19 litres per litre of beverages we produce
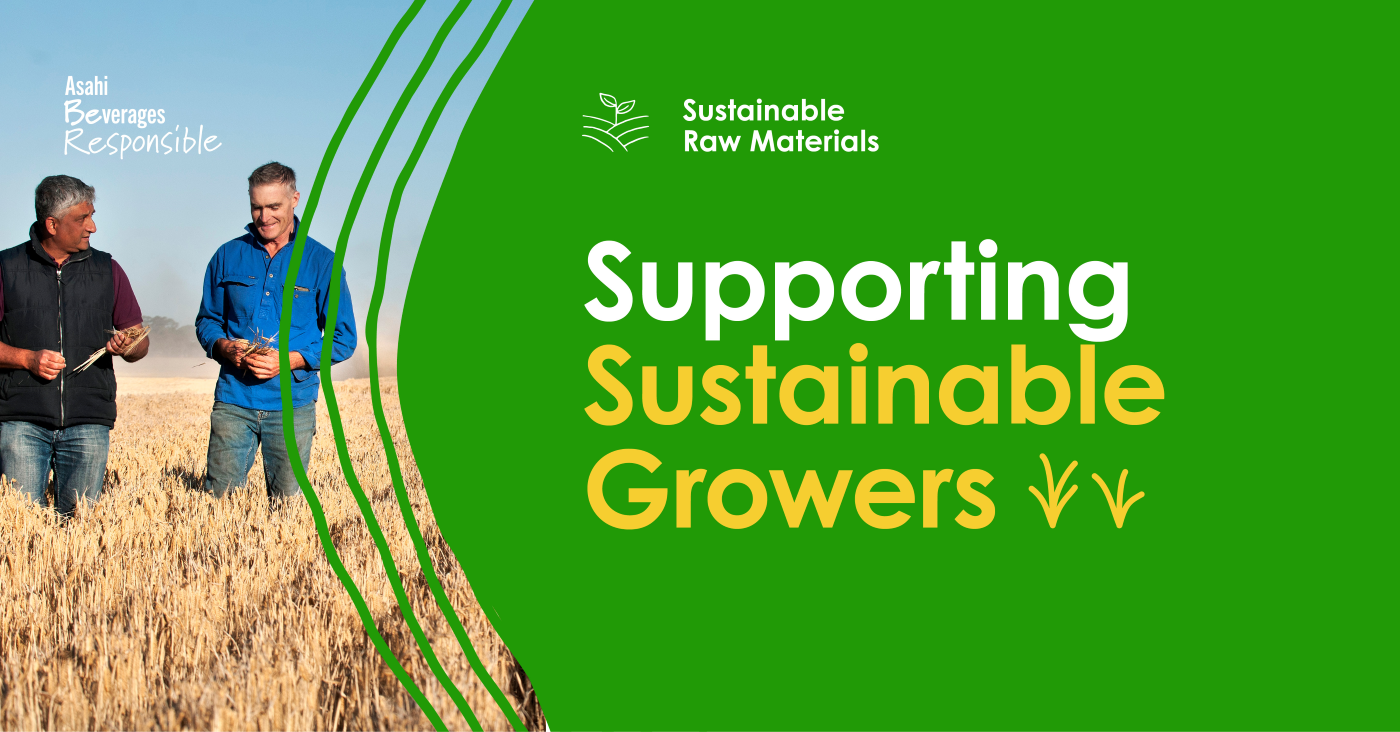
Sustainable Raw Ingredients
The best beverages are made with the best raw ingredients such as local barley, sugar and hops.
However, our sourcing choices can impact our environment and human rights.
That’s why we review our supply chain to mitigate risks and support environmentally sustainable growing practices. We are also committed to working closely with local growers who are leaders in land, environment and quality management.
We are committed to respecting internationally recognised human rights and oppose all forms of slavery, both within our activities and undertakings and within our supply chain. Our latest Modern Slavery Joint Statement can be found in the online register and our Human Rights Policy can be accessed here.
What we are targeting - our Environmental Sustainable Raw Ingredients goals:
- Review key raw materials across our supply chain to mitigate climate risks, water risks and management of environmental loads-priority
- Work closely with growers and support farms to drive best practice land, environment and quality management
Some of our initiatives so far:
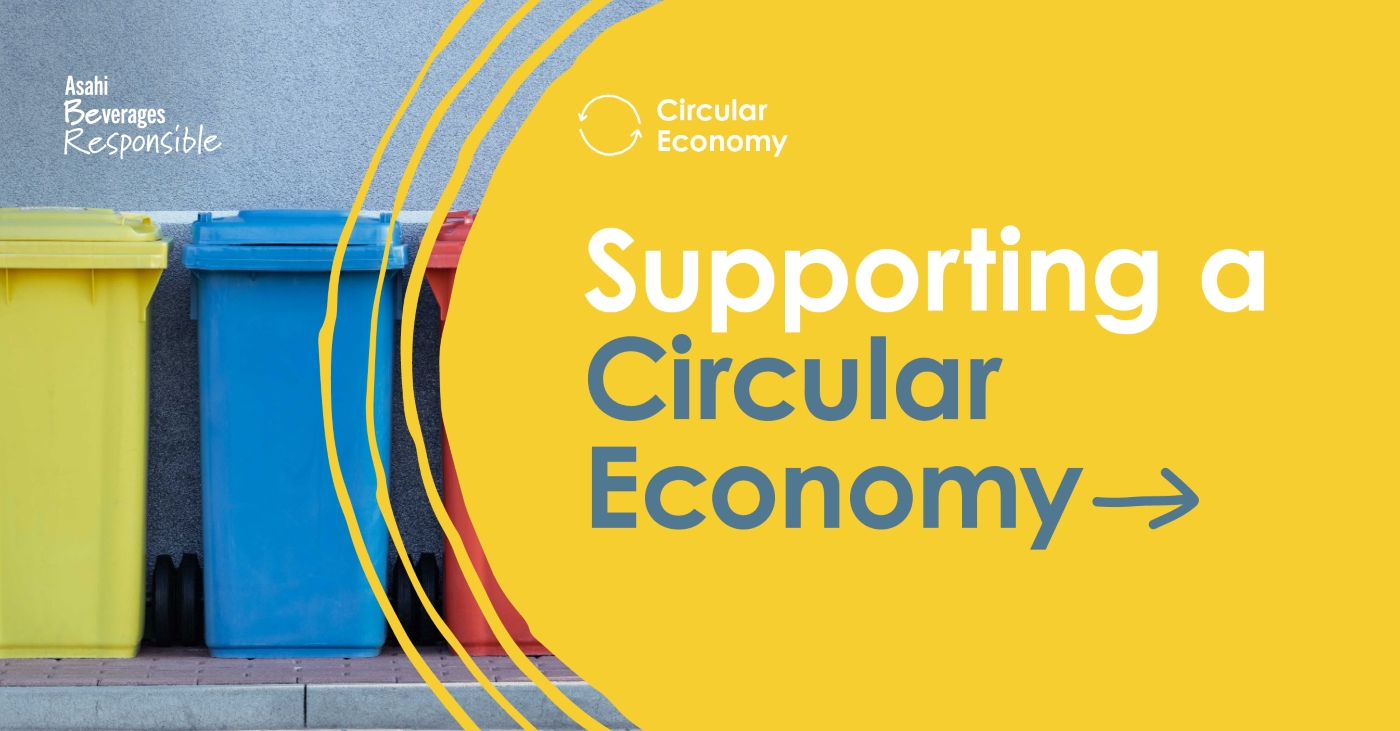
Circular Economy
Not enough recycled plastic is being produced in Australia, which is why we helped build a new facility in NSW.
Circular Plastics Australia (PET) is a joint venture partnership between Pact Group, Cleanaway Waste Management Ltd, Asahi Beverages and Coca-Cola Europacific Partners (CCEP).
The Circular Plastics Australia (PET) facility in Albury is fully operational and has the capacity to recycle the equivalent of 1 billion 600 ml PET plastic bottles each year. The aim is to then convert this into new recycled PET including bottles, helping secure Asahi Beverages’ supply. A second facility in Altona North, Victoria, commenced operations in December 2023.
In addition, it is our aim that no waste from our manufacturing sites and warehouses will go to landfill by 2030, other than unavoidable residual waste. Instead, we will work with suppliers and staff to divert waste and improve recycling rates. We will also seek to collect and convert by-products into a wide variety of valuable materials via new partnerships and investments in new technology.
What we are targeting - our Circular Economy goal:
-
Towards zero waste to landfill by 2030 at our manufacturing sites
Some of our initiatives so far:
- Victoria’s biggest PET plastic bottle recycling plant opens for business in Melbourne
- World-class recycling plant opens in Albury-Wodonga
Our Environment Policy sets out our company commitments and strategies. Read the document here.